Read the latest White Paper on how to avoid recalls in the Pre-Packed Food Industry.
The White Paper also includes examples of recent recalls and how they could easily have been avoided.
This informative paper has been brought to you from Bizerba. Global industry leaders in Checkweigh, Logistic and Inspection systems.
Highlighting the checkweigher and inspection systems from Bizerba. How they can help you avoid unnecessary recalls or production failures within the food industry.
Introducing the new CWPmaxx. The latest inspection system by Bizerba. How using the CW checkweigher and inspection range can reduce if not eliminate product recalls within the food industry.
The White Paper Covers
- Trends and Developments in the Food Industry.
- Recall Scenarios (Types and Causes).
- The Impact of Recall Campaigns.
How can Bizerba Prevent Recall Campaigns?
Sample text from the paper.
Trends and Developments in the Food Industry Food packaging becomes more and more important all over the world.
For instance, the sharply growing trend towards meals individually produced for specific customers results in an increasing need for individual packaging. At the same time, the consumption of ready meals is becoming more widespread. Health and safety are of special importance for consumers.
In addition to preserving and protecting food products before they are eaten, packages must provide useful and reliable information for risk-free consumption of the product. Therefore, a control system forming a part of the manufacturer’s food safety and risk analysis is more important than ever. Among other purposes, manufacturers are using these systems to prevent any bacterial or allergic risks which could occur if the product had an inappropriate package. If it was wrongly labelled or printed or if the package is sealed or closed inadequately.
This is especially true for products marketed under a specific brand because any faults will have a detrimental effect on the brand’s reputation. Often, incidents in the food and beverage supply chain create an enormous media response. Consequently, consumers become increasingly cautious when it comes to processed products and the quality of their food. While they demand tasty products, they are not willing to make any trade-off regarding health and food safety.
White Paper – More on product recalls
Against this backdrop, the reluctance to return faulty products to the manufacturer is decreasing noticeably. The number of recalls of ready meals has dramatically grown in recent years. In today’s supermarkets, consumers come across packages with incorrect or wrongly placed labels, open closures or seals, leaking films or inappropriate packing material or they discover expired products.
In the worst case, consumers will not notice these faults until they arrive at their homes. Many consumers do not think about complaining to the retailer or manufacturer because they are uncertain about the procedure of the reclamation process or because they assume that it is too late to return the product. Nonetheless, their dissatisfaction with the incident will linger in the background without the manufacturer’s knowledge.
Nonetheless, these so-called ‘unknown complaints’ have far-reaching consequences. The consumers concerned tend to discuss their dissatisfaction within their own circles and even go as far as to warn third parties via the internet. There is no way for the manufacturer to react and restore the customer’s faith in the products or brand. Some food producers (especially manufacturers of branded goods) therefore overreact if they face a complaint.
To compensate for the damage, they generously give away products, vouchers or other high valued items in order to make the customer happy again. After all, for each returned product there will be a number of unknown complaints resulting in an incalculable damage to the company’s reputation.

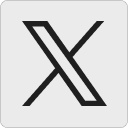


